La calidad del cable es el principal factor que debe tenerse en cuenta a la hora de elegir los cables eléctricos. Los cables de calidad inferior pueden provocar fallos de cortocircuito en los equipos eléctricos e incluso accidentes de incendio. Los defectos en la calidad de los cables se encuentran principalmente en las siguientes áreas.
Fallo de reticulación (alargamiento térmico)
Si el grado de reticulación no cumple la norma, el cable no puede cumplir los requisitos de la temperatura de trabajo de 90°C. Uno de las causas de los fallos de reticulación es que la fórmula no está cualificada. Los tipos de compuesto no están bien proporcionados y deben resolverse ajustando la fórmula.
El segundo es el proceso de vulcanización inadecuado, como la baja presión de aire, la rápida velocidad de la línea, el alto nivel de agua de refrigeración y otros factores. También es posible que existan varias causas al mismo tiempo. Hay que detectar las causas específicas y luego eliminarlas.
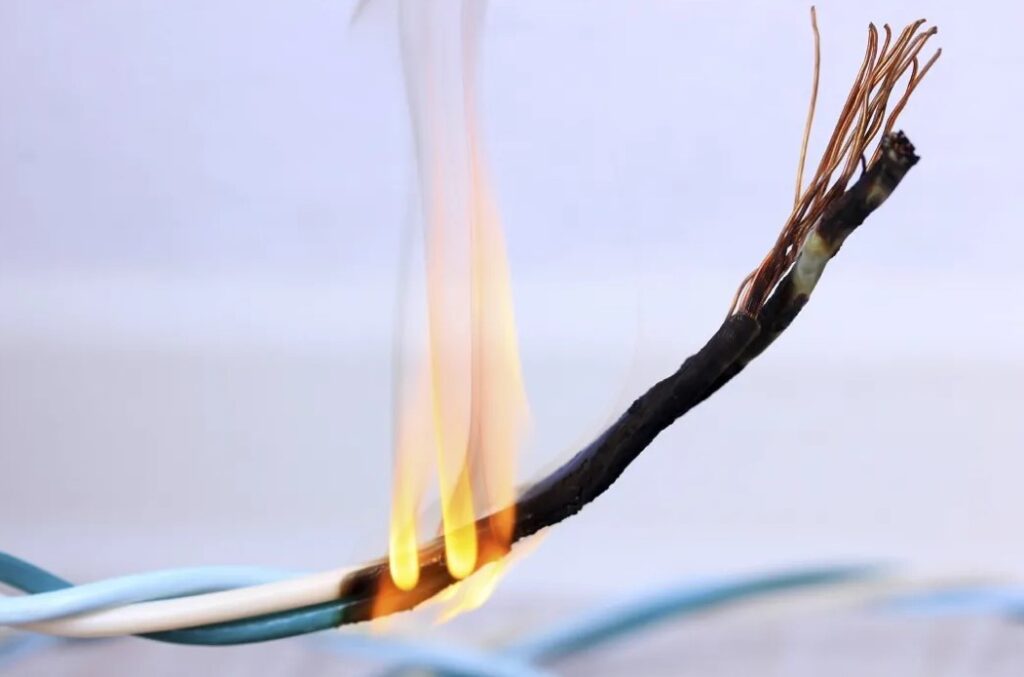
Defectos de estructura y apariencia
Espesor del aislamiento
El punto más fino del espesor del aislamiento es inferior al valor mínimo especificado en la norma, o el espesor medio es inferior al valor nominal. Los fallos en el grosor del aislamiento se deben a la velocidad de la línea, a la pequeña salida de la extrusora, a la selección inadecuada de los moldes, etc. La solución es reducir la velocidad de la línea y ajustar el tamaño del molde.
Excentricidad
La excentricidad se debe a que el molde no está correctamente ajustado o a que tras el ajuste, el control de la suspensión ha cambiado. La solución es tratar de mantener estable el control del voladizo durante el proceso de conducción.
Impurezas
La mayoría de las impurezas de los materiales aislantes y semiaislantes se mezclan durante el mezclado y la adición de materiales. Debe prestarse una estricta atención a la limpieza del material durante el funcionamiento para evitar que se mezclen impurezas externas. Otra impureza son los grumos chamuscados, que afectan al rendimiento y la vida útil del cable. Para evitarlo, el proceso de mezcla y extrusión debe estar estrictamente controlado para impedir que se chamusque.
Burbujas de aire
Hay dos posibles causas de las burbujas de aire en el aislamiento. Uno de ellos se produce durante la extrusión. La solución consiste en hacer coincidir el molde adecuado. La razón principal de las burbujas en el apantallamiento es que hay humedad en la materia prima, que debe secarse antes de la extrusión.
La segunda es un enfriamiento inadecuado, que da lugar a un círculo de burbujas alrededor de la circunferencia equidistante del núcleo del alambre. La forma de evitarlo es subir el nivel del agua y bajar la temperatura del agua de refrigeración.
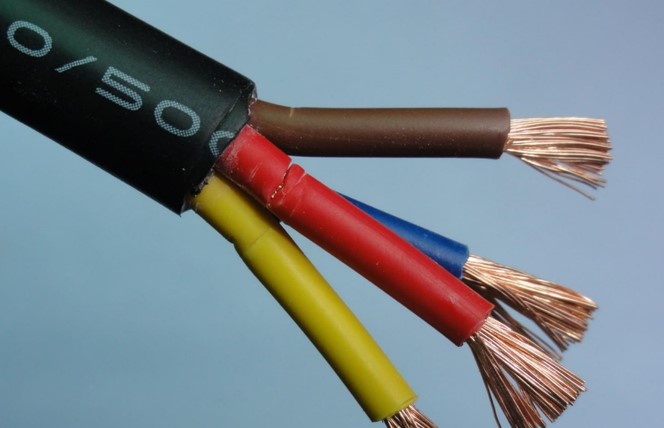
Fallos de rendimiento
Descarga libre y pérdida dieléctrica
Las causas de los fallos por descarga libre y pérdida dieléctrica son complejas. Está estrechamente relacionado con el apantallamiento, el aislamiento impurezas y el rendimiento de las materias primas. El método de eliminación consiste en mantener la materia prima limpia y producir estrictamente según el proceso.
Rotura del aislamiento del cable
Las principales causas de la rotura del aislamiento de los cables son las impurezas mezcladas con el material aislante y los daños externos. Por lo tanto, hay que evitar las impurezas en la medida de lo posible y gestionar estrictamente los productos semiacabados para evitar tropiezos y magulladuras.